
Industrial NDE
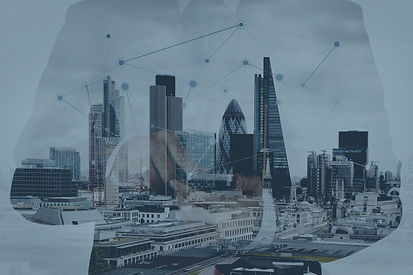
SERVICES

CORE SERVICES
-
NDE - NON DESTRUCTIVE EXAMINATION
UT – Ultrasonic Testing
MT – Magnetic Particle Testing
PT – Liquid Penetrant Testing
VT – Visual Testing
Boroscopic Inspection
MFE – Magnetic Flux Exclusion
Shear Wave
Leak Testing (Vacuum Box)
-
QA/QC NEW CONSTRUCTION
Structural Steel Inspection
High Purity Piping
Material Inspection
Civil Inspection
Architectural Inspection
HVAC Inspection
Certified Welding Inspections (CWI)
Positive Material Identification (PMI)
Contractors Documentation Verification
Witness Tests Certifications
ADDITIONAL SERVICES
-
API EQUIPMENT INSPECTION
Pressure Vessels API 510
Process Piping API 570
Aboveground Storage Tank API 653
-
Written Procedures
-
Corrosion/ Erosion Analysis
-
Consulting & Evaluation
-
Drafting and Cad Drawings
Turnarounds / Shutdowns

NONDESTRUCTIVE EXAMINATIONS
As a corporate member of the American Society of Nondestructive Testing, Inc. (ASNT) we follow the NDE methods to assure your project's quality and reliability. We have a corporate ASNT Certified Level III that, manages our NDE program and experienced NDE Level II Certified technicians perform all tests.

Ultrasonic Thickness (UT) Testing
Ultrasonic Thickness (UT) Testing
We can perform ultrasonic thickness testing on your casting, and forging, piping, plate, structural steel and pressure vessels. Also Flaw Detection technique is used to ensure conformance to specifications, identification and sizing of defects for repair as is required. Flaw detection has also been proven useful when radiography is not feasible owing to the geometry or when the thickness of the part being examined is larger or when the hazards of radiography cannot be accommodated.
INI CORP. technicians physically take thickness readings of your equipment in several keys areas to determine the actual condition.
At INI CORP., we use portable, up to date ultrasonic thickness gages and flaw detector with a wide variety of transducers.
Equipment:
Panametrics 36DL Plus UT gauge
Panametrics 37DL Plus UT gauge
Panametrics EPOCH 4
C1 Spider Crawler
We can perform automatic B-scan with the C1 “Spider” remote access ultrasonic crawler designed to allow cost effective ultrasound thickness measurements on above ground Ferro-magnetic structures without the need for costly scaffolding.



Shear Wave / Phase Array
Ultrasonic shear wave testing (UTsw) utilizes high frequency sound to locate discontinuities below the examination surface. It can be used to detect certain types of cracking and laminations in piping, plate and some cast products depending on the metallurgical properties.
High frequency sound is introduced into the material using portable equipment without making any damage. With the equipments results, the technician determines whether the item is acceptable or rejectable by interpreting the signals displayed on the instrument’s screen.
Requirements
Items to be examined with Utsw must have surfaces that are clean and free of excessive pitting, rust scale, loose paint, dirt, grease, etc. Though sand blasting is not required, surfaces generally need to be well cleaned to ensure adequate wave sound transmission.
Applications
-
Crack Detection and Sizing for In-service Components
-
Weld Acceptability Per Applicable Construction Codes
-
Vessels
-
Pipping
-
Tanks
-
Structural Elements
-


Magnetic Particle (MT) Testing
Magnetic Particle is a nondestructive method that uses both dry and wet examination, for detecting cracks and other discontinuities at or near the surface in ferromagnetic materials. Magnetic particle examination may be applied to raw material, semi-finished material (billets, blooms, castings, and forgings), finished material and welds, regardless of heat treatment or lack thereof. It is useful for preventive maintenance examination.
Equipments:
Magnetic Yokes
Magnaflux Magnetize & De-magnetize Machines 4000 amps
The reports are produced thru our TMS program electronically and in hard copy. That gives the company the opportunity to store, analyze and process the collected data.

Liquid Penetrant (PT) Testing
Liquid penetrant inspection has been an industrial testing standard for decades and remains one of the most reliable, efficient, and cost effective methods for detecting surface flaws in non-porous materials that may not be detected by standard visual inspection methods.
Ideal for locating discontinuities on material surfaces, Liquid Penetrant Inspection has few limits in size, shape, or composition of items to be inspected. We saturate the inspection surfaces with a highly penetrating dye that will enter even the smallest surface discontinuities. After sufficient penetration time, the excess dye is removed and a developing agent is applied to assist the bleed-out and contrast of dye retained in flaws for evaluation.
Equipment:
Liquid Penetrant
Developer
Cleaner

Visual Testing (VT)
One of the first, natural, methods of testing of anything we use is visual testing. Almost any specimen can be visually examined to determine correctness of size, completeness, the parts count, and the accuracy of fabrication. In many cases, visual inspection will eliminate the need for more sophisticated nondestructive testing of the specimen. Visual testing may locate portions of the specimen that should be inspected further by another technique.
Application of visual testing requires visual contact with the portion of the specimen to be inspected, adequate illumination of the specimen, and some specifications for the specimen.
Our technicians are prepared to give you the best possible assessment of your equipment with this technique.
Equipment:
Spot Lights
Magnifying Lens
Additional requirements
Technician's Visual eye acuity

BOROSCOPIC INSPECTION

Magnetic Flux Exclusion (MFE)
INI CORP. utilizes Hawkeye and IRis Boroscopes to inspect hard to reach areas, inspect high purity welds. We have highly trained technicians to inspect your piping or equipment with the capability to store electronically the obtained data for future reference or analysis.
​


Leak Testing (Vacuum Box)
Tanks floors can be tested using the vacuum box technique that allows determining leaking steel plates, welds or joints. INI CORP. can perform this vacuum box test using its 30” straight & cornered boxes.
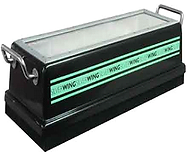


API EQUIPMENT INSPECTION
OSHA’s Process Safety management regulation, Mechanical Integrity (29 CFR 1910.119) requires facilities to conduct periodic inspections and tests on process equipment covered by the rule. In addition, this rule requires proper training and certification of personnel performing these tasks. API offers three Inspector Certification Programs which have become the industry's standard.
Most of our inspectors are API Certified Inspectors 510, 570 & 653.

API 570 Piping
This is the major industry standard used to inspect, evaluate, repair, and rate piping systems and it has become an integral part of most Process Safety Management of the mechanical integrity inspection programs.
Our API 570 inspections and engineering evaluations provide NDE data, visual inspection and engineering assessment that include maximum working pressure (MAWP) and remaining life calculations.


API 653 Tanks
This inspection code is the one that handles the inspection, data evaluation and repair of aboveground storage tanks.
Some of the techniques we used to accomplish the inspection are:
Ultrasonic testing (UT)
Liquid Penetrant (PT)
Visual testing (VT)
Magnetic Penetrant testing (MT)
Leak testing (Vacuum Box) Magnetic
Flux exclusion (MFE)
INI CORP. can provide magnetic Flux Exclusion for inspecting above ground storage tank floors. This process is a quick and accurate method for detecting bottom side corrosion. It is usually cost – effective and advantageous to employ MFE examination to large carbon steel storage tanks (over 20’ in diameter).
The basic principle involved in this tool includes the saturation of the floor plate with a magnetic flux and the detection of flux leakage. For this particular application, a magnetic bridge is used to introduce as near a saturation of flux as possible in the inspection material between the poles of the bridge. Any significant reduction in the thickness of the plate, will result in some magnetic flux being forced into the air around the reduction. This area is physically marked up on the tank and the remaining wall is verified with ultrasonic techniques utilizing either A or B Scan.
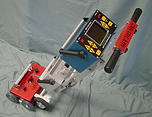

API 510 Pressure Vessels
The API 510 inspection standard evaluates the condition for service of the pressure vessels. All inspections are in accordance with the ASME Section VIII Boiler & Pressure Vessel Code. Our inspectors review and evaluate the data in order to give the customer an engineering evaluation with complete CAD drawings, TML, corrosion rates, life expectancy of the equipment, maximum temperature & pressure calculations and recommendations.
​
Of the various conventional and advanced nondestructive examination (NDE) methods, five are widely used for the examination of pressure vessels and tanks by certified pressure vessel inspectors. These are:
-
Visual Examination (VT)
-
Liquid Penetrant Test (PT)
-
Magnetic Particle Test (MT)
-
Ultrasonic Test (UT)


Industrial NDE & Inspection Services
Industrial NDE & Inspection Services can establish a mechanical integrity program suitable to your needs and their resources that will comply with the OSHA 29 CFR 1910.119 and also keep up to speed with your equipment.
INI CORP. can provide the following personnel to support this effort:
-
Mechanical Integrity Consultants
-
Field Draftsman
-
MI Project Managers
-
Data Entry Personnel
-
API Certified Inspectors
-
AWS Certified Inspectors
-
NDE Training Instructors
-
NACE Certified Inspectors
-
Positive Material Identification Techs.
-
Thermograph (Infra Red) Technicians
-
Instrumentation & Electrical Inspectors
-
Rotating Equipment Inspectors
-
Cooling Tower Inspectors
-
CAD Drafters
-
Administrative Personnel